Spectrum Logistika is a transport and logistics company with over 12 years experience in the Baltic States and Middle Asia. They provide a number of value added logistics services like warehousing, customs clearance, acceptance, collection, sorting, packing and labeling of goods.
The Problem
Before partnering with ACI, Spectrum Logistika faced several critical challenges listed below:
1. Loading Dock Congestion at Peak Times
Bundles of cargo were kept in the docks area for inspection and labeling, which in turn created a backlog and overloaded the inspection zones. This bottleneck slowed down forklifts creating warehouse traffic jams.
2. Inefficient Inspection Processes
Warehouse employees had to hand-measure boxes (yes, we are talking about using the good old Stanley tape measure) and manually deliver results to WMS software, consuming valuable time and resources.
3. Prolonged Truck Loading Times
Without precise measurements of boxes and pallets (due to under-pressure operations staff), truck loading operations were slow, resulting in half-empty loads and lost time.
4. Frequent Claims for Cargo Damages
Received numerous damage claims from customers and lacked the means to effectively defend themselves.
5. Cargo Arrival Report Absence
Had no established way of reporting incoming cargo with all necessary details, including 360-degree photos, dimensions, package types, damages, and suspicious cases. This often led to double-checks upon clients' requests for more data about the cargo.
In today's fast-paced logistics industry, efficiency and accuracy are paramount. Warehouses are the heart of logistics operations, where even minor inefficiencies can lead to significant time and cost overruns. At ACI, we are dedicated to streamlining streamlining the process to make our customers' lives easier.
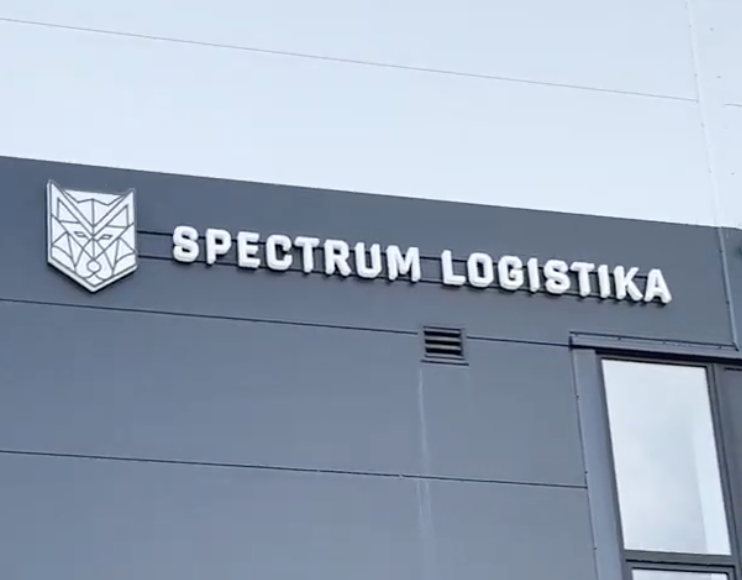
The Solution
ACI' s SmartStand was designed to address those common warehouse issues listed above. The SmartStand is an advanced, automated system that integrates seamlessly into existing warehouse operations, providing real-time data and insights.
Key Features used by Spectrum Logistika include:
1. Automated Measurement & Inspection
The SmartStand automates the measurement of boxes and pallets, providing accurate dimensions and volume calculations instantly.
2. Damage Recognition
The system automatically identifies and records any damages to the cargo, providing visual evidence and detailed documentation.
3. Package Type Recognition
The SmartStand technology recognises and categorises different package types, ensuring accurate handling and storage procedures.
4. Real-Time Data Integration
Measurements and inspection data are integrated into the warehouse management system in real-time.
5. Photo and Documentation
Each cargo load is documented with photos, measurements, and weights, creating a comprehensive master file for each shipment.
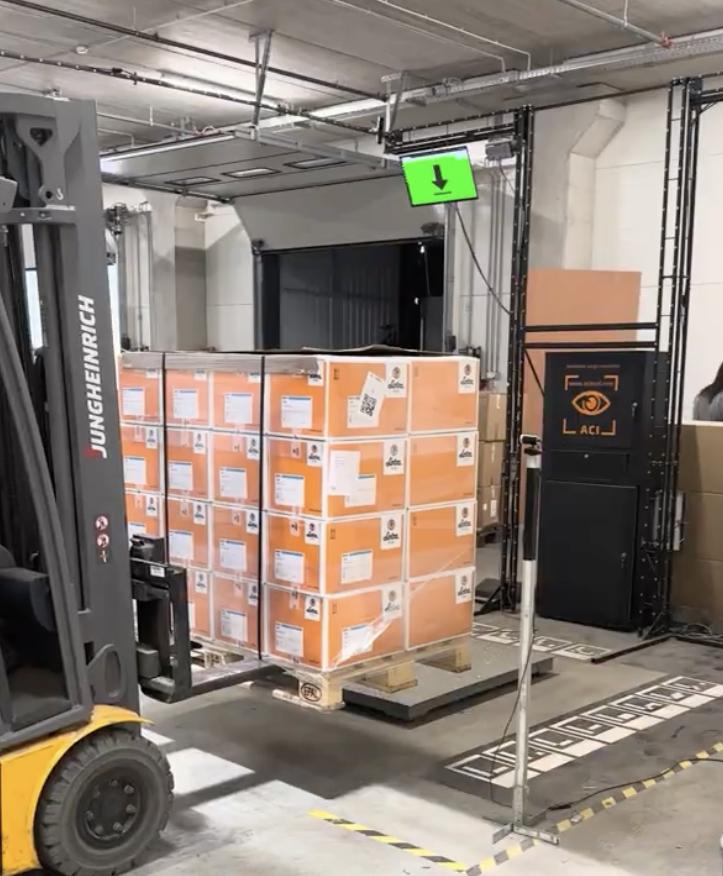
The Results
Transformational Impact on Spectrum Logistika. After implementing the ACI SmartStand, Spectrum Logistika experienced significant improvements in its operations:
1. Elimination of Damage Claims
Since the implementation of the SmartStand, Spectrum has not received any claims for cargo damages. The precise measurement, damage recognition, and documentation provided by the SmartStand enables the company to defend its shipments effectively.
2. Dramatically Reduced Inspection Time
Inspection time has been reduced from hours to seconds. Warehouse personnel can now focus on more value-creating tasks rather than walking between departments.
3. Optimised Truck Loading and Unloading
With accurate measurements and package type recognition at their fingertips, Spectrum Logistika can plan truck loading operations more efficiently & optimise unloading spaces.
4. Enhanced Customer Satisfaction
Customers receive a master file with photos, measurements, weights, and detailed damage reports for each load, providing them with convenience and peace of mind.
“We are very happy with the ACI Smartstand system, as it has enabled us to streamline our operations. The technology has reduced our cargo inspection times, completely eliminated any damage claims and at the same time improved revenue streams, as we can charge our clients more for a better and more value-added logistics (VAL) services.”
Roman Aleksejev
Terminal Manager at Spectrum Logistika
Terminal Manager at Spectrum Logistika
Commercial Effect on Spectrum Logistika Operations
Spectrum Logistika engaged most of its customers with a more visible and analysable cargo management approach thanks to ACI SmartStand and its reports.
Spectrum Logistika's customers were used to basic waybill reports that just confirmed arrival and weight.
However, when they saw the value of detailed inspections with photos, dimensions, and damage data, several upgraded to the next service tier to unlock these benefits.
Spectrum Logistika's customers were used to basic waybill reports that just confirmed arrival and weight.
However, when they saw the value of detailed inspections with photos, dimensions, and damage data, several upgraded to the next service tier to unlock these benefits.
Invitation to Warehouse Owners and Managers
ACI invites warehouse owners and managers to explore the benefits of the SmartStand solution.
We offer a no-obligation consultation to discuss how the SmartStand can transform your warehouse operations, improve efficiency, and reduce costs.
We offer a no-obligation consultation to discuss how the SmartStand can transform your warehouse operations, improve efficiency, and reduce costs.
Conclusion
The ACI SmartStand has proven to be a game-changer for Spectrum Logistika, addressing critical challenges and delivering tangible improvements in efficiency and customer satisfaction. We are committed to helping more warehouses achieve similar results.
For more information or to schedule a consultation on how we can help transform your own warehouse operations, please contact us at: sales@acitool.com