This white paper is targeted towards warehouse, operations and C-suite (CxO) managers who are curious and looking towards the future of their industry. Especially those who are interested in leveraging current AI technologies to make their logistics operations more efficient and to gain a competitive edge.
Discover 5 key trends to slashing workflow times and how to free up valuable resources in your warehouse beyond 2024.
1. Smart Warehousing and Robotics
eCommerce giant Amazon has been a leader in using AI for warehouse automation. They use AI-powered robots to pick, pack, and ship millions of items every day
2. Warehouse Space Optimisation with AI
Inditex (Spain) who own popular fashion brands like Zara and Pull&Bear. They strive for a just-in-time approach and use centralised distribution centres to maximise space efficiently.
3. Predictive Demand Forecasting
Tesco (UK) uses historical sales data and trends to predict future demand for products. This allows them to stock their warehouses with the right amount of inventory, leading to lower costs & improved client satisfaction.
4. Supply Chain Visibility and Real-Time Tracking
UPS is using AI to track shipments in real time. This allows them to identify and address any potential problems early on, which can help to improve delivery times.
5. Automatic Cargo Inspection using AI
Border security agencies are using AI to automatically inspect cargo containers. This can help to speed up the inspection process and identify contraband items.
Using alternative and fictional case study examples, let’s start by delving a little deeper into each section. We hope you find these trends valuable to your own operations!
Smart Warehousing and Robotics
AI-powered robots (or cobots) are taking over repetitive tasks like picking, packing, and sorting, boosting efficiency and accuracy.
AI-Powered Cobots are collaborative robots, designed to work alongside humans in close proximity, as known as companion robots. Cobots can autonomously navigate warehouses to retrieve items, reducing the time and effort human workers spend walking and searching for products.
Repetitive or ergonomically difficult or dangerous tasks (such as heavy lifting), or precision work can be suitable for Cobots, so that human workers can focus on more complex, value-added processes and tasks.
AI-Powered Cobots are collaborative robots, designed to work alongside humans in close proximity, as known as companion robots. Cobots can autonomously navigate warehouses to retrieve items, reducing the time and effort human workers spend walking and searching for products.
Repetitive or ergonomically difficult or dangerous tasks (such as heavy lifting), or precision work can be suitable for Cobots, so that human workers can focus on more complex, value-added processes and tasks.
Here’s a breakdown of how Cobots improve efficiencies:
Reduced Travel Time for Workers
This allows workers to focus on picking and packing tasks, improving overall productivity.
Increased Picking Accuracy
Cobots can be equipped with vision systems and sensors to precisely identify and pick items, minimizing errors and ensuring that the correct products are shipped to customers.
Ergonomic Benefits
Cobots can handle heavy or bulky items, reducing the physical strain on human workers and preventing injuries.
Faster Order Fulfillment
By automating picking and packing tasks, cobots can help warehouses process orders more quickly, leading to faster delivery times and happier customers.
Emilia the Operations Manager at Crafttable, a bustling furniture company’s fulfillment center, had an issue. Order fulfillment times were slipping. The human pickers were working long hours but struggling to keep up with demand. Repetitive tasks like picking individual items were causing fatigue.
After careful research and consultations, Maria selected lightweight, easy-to-program cobots with a gripper arm specifically designed for handling boxes. Pickers quickly learned how to interact with the cobot through a simple tablet interface. They programmed the cobot to locate specific furniture pieces based on barcodes, retrieve them from the shelves, and deliver them directly to the pickers' stations.
The results were immediate. Picking times for individual items dropped by 40%, significantly improving overall order fulfillment speed and pickers reported less fatigue.
The Crafttable success story demonstrates the power of cobots in a warehouse environment. Cobots not only boost efficiency but also improve worker safety and morale by reducing the physical strain of repetitive tasks. The human-robot collaboration creates a win-win situation for businesses and employees, leading to a more productive and positive work environment.
After careful research and consultations, Maria selected lightweight, easy-to-program cobots with a gripper arm specifically designed for handling boxes. Pickers quickly learned how to interact with the cobot through a simple tablet interface. They programmed the cobot to locate specific furniture pieces based on barcodes, retrieve them from the shelves, and deliver them directly to the pickers' stations.
The results were immediate. Picking times for individual items dropped by 40%, significantly improving overall order fulfillment speed and pickers reported less fatigue.
The Crafttable success story demonstrates the power of cobots in a warehouse environment. Cobots not only boost efficiency but also improve worker safety and morale by reducing the physical strain of repetitive tasks. The human-robot collaboration creates a win-win situation for businesses and employees, leading to a more productive and positive work environment.
Warehouse Space Optimisation with AI
AI analyses data to dynamically adjust warehouse layouts and storage, maximising space utilisation and minimising picking times. This ensures efficient use of every square metre in the warehouse.
AI can be used to optimise warehouse space.
AI can be used to optimise warehouse space.
Here’s a breakdown of the process:
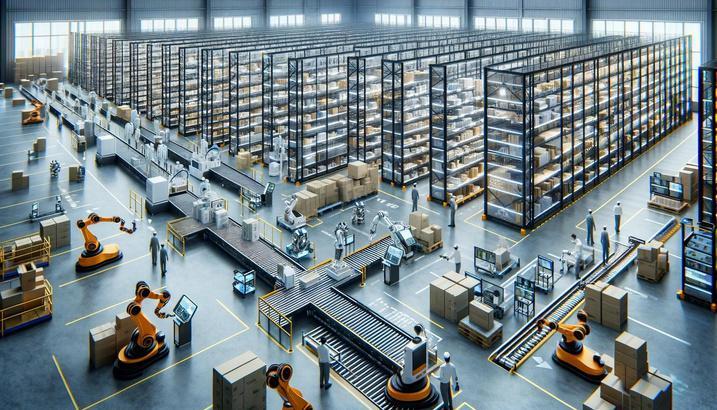
Data Collection
AI systems gather data from various sources in the warehouse, including product dimensions, historical sales data, and sensor readings from inventory.
Analysis of Data
The AI analyses this data to identify patterns and trends. For example, it can identify which items are frequently picked together or which items are slow-moving.
Space Optimisation Recommendations
Based on its analysis, the AI recommends changes to the warehouse layout to improve space utilisation. This might involve reorganising shelves, designating specific zones for high-demand items, or implementing vertical storage solutions.
Real-time Optimisation
AI can continuously monitor warehouse operations and suggest adjustments to the layout in real-time. This ensures that the warehouse remains optimised as inventory levels and picking patterns change.
By following these steps, AI can help warehouses maximise their use of space and improve overall efficiency. This can lead to significant cost savings and improved picking times.
Fridgey Ltd business was booming after launching their new line of eco-friendly fridges. But their existing warehouse was bursting at the seams.
Traditionally, warehouse optimisation involved manual analysis of spreadsheets and gut feeling. But Fridgey's forward-thinking CEO, Isabella, decided to explore a new approach: AI-powered space optimisation.
The company started a process with data collection. They fed historical sales data, product dimensions, and even forklift traffic patterns into a AI system.
After crunching the numbers, it delivered its verdict: a complete warehouse layout overhaul. The AI recommended a dynamic storage system with designated zones for fast-moving fridges and a modular shelving system that could be adjusted based on demand.
The new system utilised the warehouse's vertical space more effectively, maximising sqm usage and minimising forklift travel distances. Fridgey managed to increase storage capacity and picking times dropped by 20% thanks to the optimised layout. The AI even suggested strategic placement of frequently picked items together, further streamlining the picking process. Overall, increased productivity, providing a win win for businesses and customers who benefit from faster delivery times!
Fridgey Ltd business was booming after launching their new line of eco-friendly fridges. But their existing warehouse was bursting at the seams.
Traditionally, warehouse optimisation involved manual analysis of spreadsheets and gut feeling. But Fridgey's forward-thinking CEO, Isabella, decided to explore a new approach: AI-powered space optimisation.
The company started a process with data collection. They fed historical sales data, product dimensions, and even forklift traffic patterns into a AI system.
After crunching the numbers, it delivered its verdict: a complete warehouse layout overhaul. The AI recommended a dynamic storage system with designated zones for fast-moving fridges and a modular shelving system that could be adjusted based on demand.
The new system utilised the warehouse's vertical space more effectively, maximising sqm usage and minimising forklift travel distances. Fridgey managed to increase storage capacity and picking times dropped by 20% thanks to the optimised layout. The AI even suggested strategic placement of frequently picked items together, further streamlining the picking process. Overall, increased productivity, providing a win win for businesses and customers who benefit from faster delivery times!
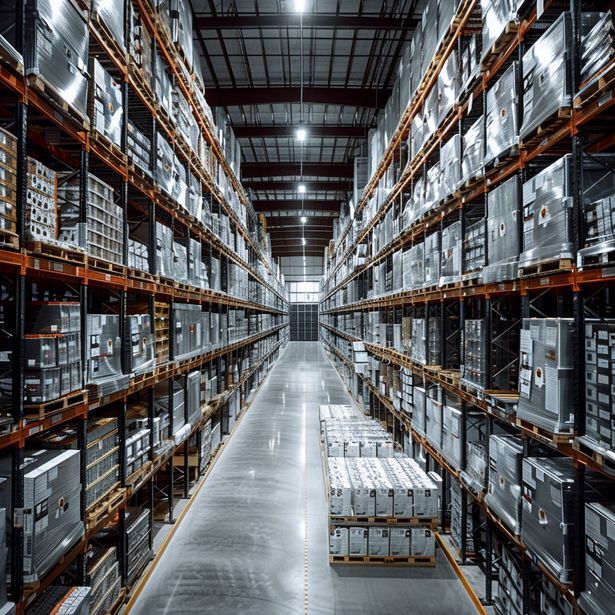
Predictive Demand Forecasting
AI helps predict future customer demand with greater accuracy. This allows warehouses to optimise inventory levels (including lower inventory holding costs), reduce stockouts by anticipating demand fluctuations, and ensure on-time deliveries, and more effective promotions leading to happier customers.
AI can be used in predictive demand forecasting. Here’s a breakdown of how it works:
Data Collection
- Historical sales data: This includes information on past sales of each product, such as quantity sold, price point, and sales trends over time.
- External data: This can include factors that might influence demand, such as weather data, economic indicators, competitor marketing campaigns, and social media trends.
Data Analysis
Statistical models and algorithms are applied to the data to identify patterns and relationships. e.g. Fitness equipment sales increase in January due to New Year resolutions.
Forecasting Future Demand
Based on the identified patterns and relationships. This forecast considers historical sales data and external factors that might influence demand.
Inventory Management
The demand forecast is used to optimise inventory levels. Warehouses can ensure they have enough stock to meet demand without overstocking or running out of popular items.
Real-time Updates
Predictive demand forecasting models are constantly updated with new data. This allows the forecast to adapt to changing circumstances and remain accurate.
Imagine a company called DandyLawns that produce and sell lawn and garden equipment. Using historical sales data, the AI model might identify that sales of the equipment tend to increase significantly in the spring and summer months. The model might also consider external factors such as weather forecasts and upcoming holidays. Based on this information, the AI model can predict that demand for equipment will be high in the coming months. This allows the company to stock up on the correct equipment in advance to meet demand and avoid stockouts.
You might be thinking the AI for Predictive Demand Forecasting is very similar to the Warehouse Optimisation and you would be correct. Although, there are some key differences.
Here's an analogy to illustrate the difference:
Imagine a warehouse as a kitchen. Warehouse optimisation is like rearranging your pantry to maximise space and efficiency, placing frequently used items within easy reach.
Predictive demand forecasting is like planning your grocery list based on past consumption, upcoming events (like a party), and even the weather forecast (grilling steaks for a summer barbecue).
While both data collection and analysis are crucial to both processes, they are ultimately used to achieve different goals within warehouse operations.
You might be thinking the AI for Predictive Demand Forecasting is very similar to the Warehouse Optimisation and you would be correct. Although, there are some key differences.
Here's an analogy to illustrate the difference:
Imagine a warehouse as a kitchen. Warehouse optimisation is like rearranging your pantry to maximise space and efficiency, placing frequently used items within easy reach.
Predictive demand forecasting is like planning your grocery list based on past consumption, upcoming events (like a party), and even the weather forecast (grilling steaks for a summer barbecue).
While both data collection and analysis are crucial to both processes, they are ultimately used to achieve different goals within warehouse operations.
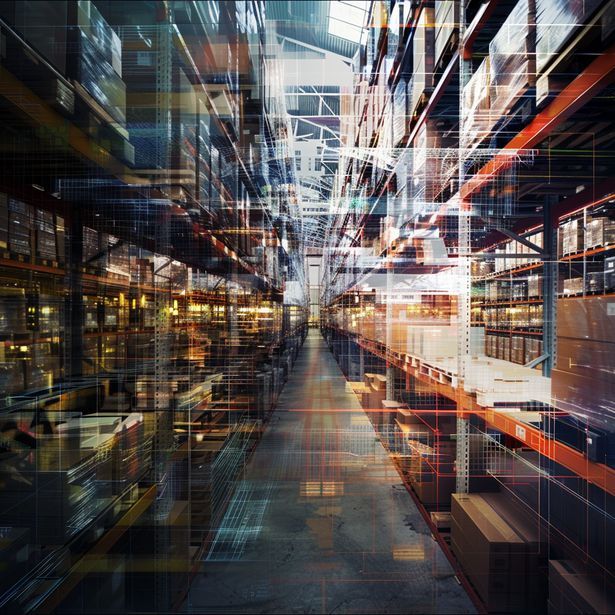
Supply Chain Visibility and Real-Time Tracking
AI provides real-time tracking of goods throughout the supply chain. This allows for faster issue identification, improved decision-making, and better transparency.
Here's a breakdown of the benefits:
Improved Efficiency
Real-time tracking allows logistics companies to pinpoint the exact location of their shipments at any given time. This eliminates the need for manual tracking and phone calls, streamlining operations and reducing overall transportation costs.
Faster Issue Identification and Resolution
With real-time visibility into the supply chain, logistics companies can identify potential problems early on, such as delays, damages, or misplaced goods. This allows them to take corrective action, ensuring on-time deliveries.
Better Decision-Making
Access to real-time data empowers logistics companies to make data-driven decisions. They can optimise delivery routes based on traffic conditions, adjust inventory levels based on shipment locations, and proactively address any potential issues that might arise.
Enhanced Customer Satisfaction
Real-time tracking allows logistics companies to keep their customers informed about the status of their shipments. This builds trust and improves customer satisfaction.
Increased Transparency
Supply chain visibility provides a holistic view of the entire supply chain process. This allows companies to identify areas for improvement and to collaborate more effectively.
Overall, supply chain visibility and real-time tracking are essential tools for modern logistics companies by improving efficiency, reducing costs, and enhancing customer satisfaction.
In the bustling world of Veloway, keeping up with demand for their high-performance cycles was a constant challenge. Their supply chain, a complex web of international manufacturers and distributors, often led to frustrating delays and a lack of transparency. Inventory levels were a guessing game, and pinpointing the location of specific bikes during transport was like searching for a needle in a haystack.
Frustrated by these inefficiencies, Veloway’s COO, Imogen, decided to leverage the power of AI and real-time tracking. The company partnered with a leading logistics solutions provider to implement a comprehensive AI-powered supply chain visibility system.
The first step involved data collection. They integrated data from various sources, including:
All this data flowed into a central AI platform. Powerful algorithms then worked their magic.
The results were transformative. Veloway’s customer satisfaction soared as delivery times became more predictable. Inventory management became streamlined, reducing the risk of overstocking or understocking. The AI even helped identify faster shipping routes, leading to cost savings.
By harnessing the power of data and intelligent algorithms, Veloway gained a clear picture of their entire supply chain, optimised operations, and delivered a superior customer experience. It's a win-win for everyone.
In the bustling world of Veloway, keeping up with demand for their high-performance cycles was a constant challenge. Their supply chain, a complex web of international manufacturers and distributors, often led to frustrating delays and a lack of transparency. Inventory levels were a guessing game, and pinpointing the location of specific bikes during transport was like searching for a needle in a haystack.
Frustrated by these inefficiencies, Veloway’s COO, Imogen, decided to leverage the power of AI and real-time tracking. The company partnered with a leading logistics solutions provider to implement a comprehensive AI-powered supply chain visibility system.
The first step involved data collection. They integrated data from various sources, including:
- Manufacturing plants: Real-time production data on bikes being assembled and shipped.
- Shipping companies: GPS location data of containers carrying VelowayBikes.
- Warehouses: Inventory levels and status updates for bikes in storage.
All this data flowed into a central AI platform. Powerful algorithms then worked their magic.
- Real-time Tracking: The AI analysed GPS data to pinpoint the exact location of every container carrying Veloway Bikes. This allowed the company to track their inventory throughout the journey, from factory to warehouse to customer.
- Predictive Analytics: AI analysed historical data on production times, shipping routes, and potential delays at customs. This allowed Veloway to predict potential bottlenecks and proactively take corrective actions, such as rerouting shipments or adjusting production schedules.
- Inventory Optimisation: With real-time data on inventory levels across warehouses, Veloway could optimise stock allocation. They could ensure popular models were readily available in high-demand regions, reducing stockouts and lost sales.
The results were transformative. Veloway’s customer satisfaction soared as delivery times became more predictable. Inventory management became streamlined, reducing the risk of overstocking or understocking. The AI even helped identify faster shipping routes, leading to cost savings.
By harnessing the power of data and intelligent algorithms, Veloway gained a clear picture of their entire supply chain, optimised operations, and delivered a superior customer experience. It's a win-win for everyone.
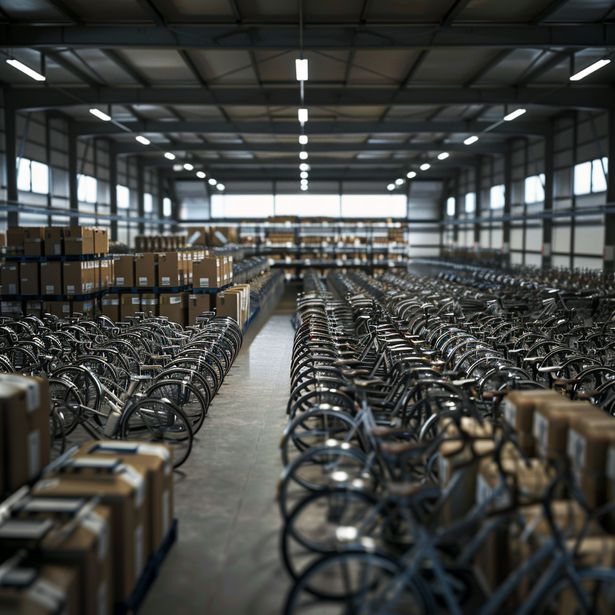
Automatic Cargo Inspection using AI
Visual quality control systems can capture measurements and any cargo damage providing quick and detailed reporting without the need for human inspection.
Historically, traditional cargo inspection relied on very menial and manual tasks of measuring and inspecting boxes, checking the volume and spotting any damage.
Historically, traditional cargo inspection relied on very menial and manual tasks of measuring and inspecting boxes, checking the volume and spotting any damage.
Here's a breakdown of the benefits:
Increased Efficiency
Manual cargo inspection is a time-consuming and labour-intensive process. AI-powered systems can inspect cargo much faster, with stock flowing into and out of the warehouse quicker.
Improved Accuracy
AI systems are trained on massive datasets of images and can detect discrepancies between shipping packing lists and actual cargo with exceptional precision.
Reduced Costs
Faster inspections lead to quicker cargo clearance, reducing fees and fewer errors in cargo declaration can minimise fines and penalties.
Improved Data Collection
Computer vision systems can generate detailed reports on the contents of each pallet. This data can be valuable for businesses, providing insights into packaging efficiency and potential areas for cargo optimisation and helping fight against damage claims.
Overall, AI-powered cargo inspection offers a significant advantage for logistics companies.
By streamlining the inspection process, improving accuracy, and reducing costs, AI technology, machine learning and computer vision systems all contribute to a more efficient and secure global supply chain.
FancyTech Ltd, a renowned importer of high-end electronics, was facing mounting frustration at their warehouse. The manual inspection process for incoming shipments was slow, tedious, and error-prone. Long lines of cargo pallets awaited inspection, causing delays and impacting their ability to deliver the latest gadgets to eager customers.
Eva, the company’s Director of Operations, knew there had to be a better way. Manual inspections were a bottleneck, straining their resources and hindering their ability to scale their business. She started exploring innovative solutions and came across an AI-powered computer vision system. Intrigued, Eva delved deeper. The system comprised several key components:
Eva was impressed. This system offered several significant advantages:
Eva convinced the company’s leadership to invest in the system. The results were remarkable. Inspection times plummeted by 70%, leading to faster product delivery and happier customers.
By leveraging cutting-edge technology, companies can streamline cargo workflows, improve efficiency, and gain a significant edge in today’s competitive global market.
By streamlining the inspection process, improving accuracy, and reducing costs, AI technology, machine learning and computer vision systems all contribute to a more efficient and secure global supply chain.
FancyTech Ltd, a renowned importer of high-end electronics, was facing mounting frustration at their warehouse. The manual inspection process for incoming shipments was slow, tedious, and error-prone. Long lines of cargo pallets awaited inspection, causing delays and impacting their ability to deliver the latest gadgets to eager customers.
Eva, the company’s Director of Operations, knew there had to be a better way. Manual inspections were a bottleneck, straining their resources and hindering their ability to scale their business. She started exploring innovative solutions and came across an AI-powered computer vision system. Intrigued, Eva delved deeper. The system comprised several key components:
- 360-degree Cameras: These high-resolution cameras were installed taking in a birds eye view from above from 4 different angles, capturing acomplete 360-degree digital image of the cargo on pallets.
- AI-powered Image Recognition: The captured images were then fed into a powerful AI image recognition system. The AI, trained on a massive dataset of labeled images, could identify individual items within the pallet, exact quantities, and even detect any signs of damage.
- Automated Reporting: Once the AI analysis was complete, an automated report was generated. This report detailed the contents of the cargo, highlighting any discrepancies between the shipping packing list and the actual cargo.
Eva was impressed. This system offered several significant advantages:
- Increased Efficiency: Automatic Cargo Inspection significantly reduced inspection times. Containers that previously took hours to inspect manually could now be cleared within minutes.
- Improved Accuracy: AI-powered image recognition reduced human error in the inspection process. The system could detect even minor discrepancies that might be missed by human inspectors.
- Reduced Costs: Faster inspections meant less labour time. This translated to lower fees and faster product delivery, reducing overall logistics costs.
Eva convinced the company’s leadership to invest in the system. The results were remarkable. Inspection times plummeted by 70%, leading to faster product delivery and happier customers.
By leveraging cutting-edge technology, companies can streamline cargo workflows, improve efficiency, and gain a significant edge in today’s competitive global market.
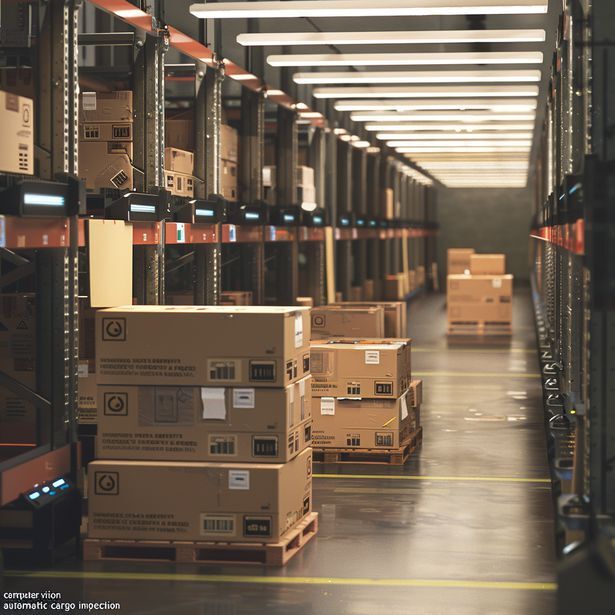
Conclusion
In summary, the AI trends covered in this document all have a common appeal to companies who are prepared to invest in the technology.
AI is revolutionising businesses by slashing costs, freeing up employees for higher-level thinking, and boosting productivity. Imagine your team empowered by AI – Are you ready to join the transformation? To learn more, please contact the ACI team at sales@acitool.com